CERAMICA
Il termine ceramica deriva dal nome greco dell'argilla (kéramos)
e in origine indica qualsiasi manufatto di argilla; è invalso,
tuttavia, l'uso di riservare la parola ceramica soltanto al vasellame
smaltato o fornito di rivestimento e di adoperare invece il termine
terracotta (agg. fittile, dal lat. fictilis) per indicare tutti
gli altri oggetti prodotti con l'argilla (statuette, decorazioni
architettoniche, mattoni, tegole etc.).
La produzione vascolare nacque dall'osservazione, verosimilmente
casuale, della plasticità e resistenza dell'argilla; l'uomo
infatti si accorse che l'argilla cruda poteva essere facilmente
modellata e che, avvicinandola ad una fonte di calore, si consolidava
mantenendo la forma che le era stata data; ben si prestava dunque
alla fabbricazione di recipienti. La tipologia della più
antica ceramica mostra il ripetersi di forme ovoidi e tondeggianti;
il che sembra dimostrare che i primi vasi di argilla siano derivati
dall'imitazione di modelli esistenti in natura (buche e pietre
concave o legno e zucche appositamente cavati all'interno) inizialmente
usati per la raccolta di liquidi e per la conservazione di cibi.
L'apparizione della ceramica risale al Neolitico, coincide cioé
col momento di passaggio dal nomadismo alla sedentarizzazione
e dall'economia di sussistenza basata sulla caccia, sulla pesca
e sulla raccolta, all'economia produttiva fondata sulla cerealicoltura
e l'allevamento. I primi prodotti, modellati a mano e cotti in
forni rudimentali, furono dapprima decorati con semplici incisioni
o impressioni, poi dipinti. Col passare del tempo si affinarono
le tecniche di modellazione e di cottura e si arricchì
il patrimonio formale e decorativo.
IMPASTO
Dagli impasti molto grossolani con cui furono realizzati i vasi
più antichi, ottenuti direttamente con l'argilla estratta
dalle cave senza operare nessuna scelta qualitativa, si passò
ad impasti meno rozzi che contenevano argilla più "pulita",
fino ad arrivare alla c.d. argilla figulina, cioé ad un
amalgama che, prima della modellazione, veniva sottoposto ad una
serie di operazioni finalizzate all'eliminazione di qualunque
particella estranea (pietruzze e detriti vari) presente nelle
zolle di argilla. I sistemi adoperati per la depurazione furono
vari: la setacciatura, la levigazione in acqua corrente e la sedimentazione
in acqua ferma. L'ultimo sistema, molto semplice e poco faticoso,
fu probabilmente quello più usato. L'argilla, resa praticamente
liquida con l'aggiunta di una notevole quantità d'acqua,
si lasciava decantare in grosse vasche per un lungo periodo di
tempo durante il quale tutte le impurità si depositavano
sul fondo; trascorso questo periodo di tempo si procedeva al prelievo
dell'argilla superficiale depurata che veniva posta in un'altra
vasca, dove l'evaporazione dell'acqua ne determinava l'asciugatura
che si protraeva fino a quando la massa argillosa non aveva raggiunto
un grado di plasticità tale da consentirne la lavorazione.
Se l'argilla era però troppo "grassa", e cioé
molto plastica, si rendeva necessaria l'aggiunta di elementi degrassanti
quali sabbia, mica, tritume lavico e di terracotta che le conferivano
maggiore consistenza.
MODELLAZIONE
Le diverse tecniche di modellazione, che si andarono affinando
nel corso dei secoli, coesistettero nell'antichità e sono
in uso ancora oggi. La prima e più antica tecnica - la
modellazione a mano - non richiedeva ovviamente nessuna attrezzatura;
era sufficiente rendere concavo, attraverso la pressione delle
mani, un pane di argilla, che era poi ulteriormente sagomato e
rifinito.
Un sistema diverso, denominato "a colombino", prevedeva
l'avvolgimento a spirale di cordoncini di argilla preventivamente
preparati, che via via andavano appiattiti all'interno e all'esterno
in modo da saldarsi gli uni con gli altri e raggiungere lo spessore
desiderato.
Da queste prime ed elementari tecniche si passò a quella
molto più precisa del tornio (gr. trochos; lat. rota figularis);
il passaggio non fu ovviamente immediato ma conobbe varie fasi
evolutive. Per evitare di doversi spostare intorno all'oggetto
che stava modellando e soprattutto per creare un vaso specularmente
identico, il vasaio pose l'argilla su un disco che, fornito di
una convessità centrale rivolta all'esterno a mo' di perno,
aveva la possibilità di ruotare su sé stesso; il
movimento veniva impresso con la mano o con i piedi. In un secondo
tempo il perno di appoggio del disco fu sostituito da un vero
e proprio asse verticale (c.d. tornio lento); rimaneva tuttavia
l'inconveniente che per far ruotare il disco necessitava la spinta
della mano che veniva così, molto spesso, distolta dal
lavoro di modellazione. Per risolvere il problema si inventò
il tornio a piede o a pedale. L'asse verticale fu, infatti, completato
in basso da una ruota che, azionata col piede, trasmetteva il
movimento al disco superiore; il vasaio, così, non solo
ebbe libere entrambe le mani ma poté mantenere costante
la rotazione e regolarne la velocità e la durata a seconda
della forma e delle dimensioni dell'oggetto da modellare. Con
questo tipo di tornio si poterono ottenere prodotti più
accurati in tempi più contenuti, anche se l'uso del tornio
non soppiantò mai completamente le altre tecniche che vennero
comunque usate in combinazione con esso. A mano, infatti, era
necessario modellare le anse e il piede del vaso che venivano
poi saldati al corpo mediante argilla diluita.
Un ultimo sistema di modellazione è quello cosiddetto a
calco, che rappresenta un'evoluzione di tipo industriale consentendo,
in tempi ancora più brevi rispetto al tornio, una produzione
in serie, di buon livello qualitativo, che non necessita di manodopera
specializzata.
Alla prima fase di modellazione seguiva la rifinitura con una
spatola, che consentiva l'eliminazione di eventuali asperità
ed imperfezioni, ed infine l'essiccamento. Esso doveva avvenire
in un luogo fresco e arieggiato per permettere all'acqua contenuta
nell'impasto di evaporare in modo lento e graduale; si trattava
di una fase molto delicata che, se condotta senza le necessarie
precauzioni, poteva compromettere il lavoro già compiuto
e provocare nel vaso rotture o fessurazioni.
In molti casi, immediatamente prima della cottura, il vaso veniva
rivestito con un sottile strato di argilla diluita (ingobbio)
che aveva il duplice scopo di eliminare la ruvidezza e l'opacità
del prodotto e in parte ridurne la porosità.
DECORAZIONE E COTTURA
La decorazione (impressa, incisa, plastica, dipinta, a rilievo),
se prevista, era eseguita prima della cottura. L'impressione e
l'incisione erano ottenute imprimendo sul vaso le dita, la valva
di una conchiglia o una cordicella ritorta, ovvero praticando,
con un arnese appuntito, delle incisioni, più o meno profonde:
linee, cerchi, spirali variamente combinate tra loro, che spesso
venivano evidenziate da incrostazioni di sostanze gessose. La
decorazione plastica si otteneva invece modellando a parte cordoni
di argilla, bugne e figurine di vario tipo che venivano incollati
sul manufatto. La decorazione dipinta oltre che monocroma (nera
o rossa), ottenuta con processi di ossidazione e di riduzione,
o bianca, ottenuta con l'ingubbiatura, poteva anche essere policroma.
In questo caso i colori, bianco, giallo e rosso, venivano sovraddipinti
sul fondo del vaso o sulle figure. La decorazione a rilievo, infine,
poteva essere realizzata con matrici, con rulli o anche con piccoli
rilievi ottenuti a parte con stampi e poi incollati sul vaso.
L'ultima fase della lavorazione era la cottura che poteva avvenire
o a diretto contatto col combustibile (focolare all'aperto) o
in fornace.

FOCOLARE ALL'APERTO O METODO A CATASTA
(da N. Cuomo di Caprio, 1988)
Nel focolare all'aperto, primitivo e
rudimentale, i manufatti posti su un terreno piano o in una fossa
erano accatastati e coperti dal combustibile. La cottura avveniva
però lentamente, a temperatura bassa e non uniforme, e
ne derivava una produzione di scarso livello qualitativo. La fornace,
che permetteva di ottenere temperature più elevate, migliore
propagazione del calore e di controllare il tiraggio, rappresentò
un grosso miglioramento. Gli scavi hanno riportato alla luce una
quantità di fornaci strutturalmente diverse tra loro, ma
che dal punto di vista tecnico si possono ricondurre a due tipi:
FOCOLARE VERTICALE da N. Cuomo di Caprio,
1988)
la fornace orizzontale e quella verticale.
La differenza consiste nel percorso seguito dal tiraggio. Nella
fornace orizzontale, dotata di una copertura a volta e di una
canna fumaria posta sul fondo della camera di combustione, il
calore, prima di uscire attraverso il fumaiolo, deviato dalla
volta, seguiva un percorso orizzontale irraggiando uniformemente
i manufatti. Questo tipo di fornace, diffusissimo in Oriente,
non ebbe, però, fortuna in Occidente dove si preferì
il tipo verticale, anch'esso indubbiamente valido ma meno avanzato.
Nella fornace verticale, infatti, priva di fumaiolo, il tiraggio
avveniva direttamente attraverso il tetto, anch'esso a volta,
ma provvisto di valvole di sfiato; il calore seguiva dunque un
percorso diretto dal basso verso l'alto e quindi l'irraggiamento
era limitato. Generalmente questo tipo di fornace era dotata di
un corridoio d'accesso denominato "prefurnio" dove veniva
accesa la legna, della camera di combustione e, immediatamente
al di sopra, della camera di cottura, dove, su un piano forato
di argilla refrattaria, sorretto da muri, pilastri o archi, venivano
impilati i manufatti da cuocere.
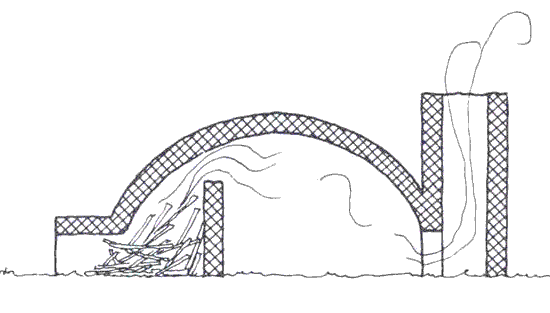
FOCOLARE ORIZZONTALE (da N. Cuomo di Caprio,
1988)
Il processo di cottura sembra si svolgesse in tre fasi. Inizialmente
i manufatti venivano messi nella fornace che, in maniera lenta
e graduale, raggiungeva i 200° C; si verificava così
la completa evaporazione dell'acqua d'impasto residua. Successivamente
la temperatura veniva innalzata fino a 1000° circa; durante
questa fase avvenivano trasformazioni chimiche che modificavano
in modo irreversibile le componenti dell'argilla. A seconda della
colorazione monocroma (rossa o nera) che si voleva ottenere era
necessaria un'atmosfera ossidante, e cioé molto ricca di
ossigeno (per la colorazione rossa) o riducente, cioé povera
di ossigeno e ricca di idrogeno e ossido di carbonio (per la colorazione
nera). Nel primo caso il fuoco era alimentato con legna secca
e il tiraggio portato al massimo con l'apertura di tutte le valvole;
l'ossigeno si combinava con i vari composti presenti nell'argilla
e dalla reazione ne derivava la formazione di anidride carbonica,
che usciva rapidamente attraverso le valvole, e di ossidi, tra
cui l'ossido ferrico che conferiva ai vasi la colorazione rossa.
Nel caso in cui si voleva ottenere vasellame a supeficie nera
si provvedeva ad alimentare la fornace con legna umida e materie
organiche grasse, nonché a limitare il tiraggio chiudendo
alcune valvole; in quest'atmosfera annebbiata e fumosa, l'ossido
di carbonio si combinava con l'ossido ferrico che diventava magnetite
(di colore nero). E' questa la trasformazione chimica che sta
alla base della creazione della cosiddetta vernice nera - che
pertanto è improprio definire vernice - e della decorazione
dei vasi greci a figure nere e rosse.
La terza e ultima fase del ciclo di cottura consisteva ovviamente
nel raffreddamento.